Post-Press
Post-press is everything that takes place after your pages have been printed on parent sheets, which is quite a bit. Now your printed sheets will be folded, cut and bound into your final project. In this section we talk about everything which comes after your printing is complete.
Folding Signatures & Collation
Once the printing is complete, the stacks of fully-printed and dried parent sheets are taken to be folded by the folding machine. Each parent sheet zooms through the machine one at a time entering into gates that are set to the proper fold size. A final fold is applied by a heavy arm, called the knife fold, that applies pressure on the fold line. The final project rolls out of the machine as a signature. The majority of projects are folded by these machines, although extremely large projects or those with unique requirements may occasionally be folded by hand.
The folded groups of pages that emerge from the folding machine are called signatures. Most projects have signatures of 16 pages (8 pages on each side of the parent sheet), but projects 6″ x 9″ or smaller may have signatures of 32 pages, and projects larger than 9″ x 12″ may only have 8 pages per signature.
Once all of the parent sheets have been folded into signatures, the stacks of signatures are taken to the collation machine, which collates the separate signatures into their proper page order. The resulting new stacks of ordered signatures are now called book blocks. Most collation machines are large enough to handle books with many hundreds of pages, but books with only two or three signatures can also be collated by hand.
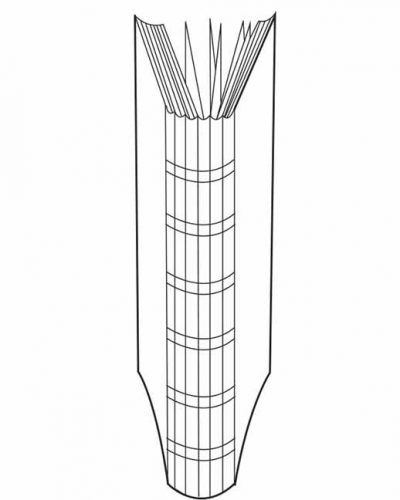
Cover Finish & Customisation
Before your book cover can be bound to the book block, the parent sheet that will become your cover needs to have any finished added to it. This includes varnishes or lamination which protect the book. You can also customise your book covers with debossing, foiling and monogramming, just like you can with notebooks, and this is the step where this takes place. Refer to our article ‘Ways to Customise‘ for more information on these.
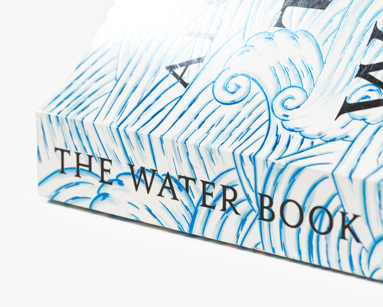
Varnish
A varnish is a liquid finish applied on the printing press following the same process as if it were an ink. The varnish style usually matches the coating of your paper (gloss or matte) and protects the ink on your cover.
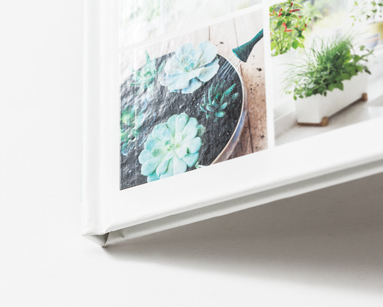
Lamination
Lamination is a film applied by a machine that glues a roll of lamination to the cover, which is subsequently polished. This finish is the best for protection and is used on thicker cover options, perfect bound and case bound books.
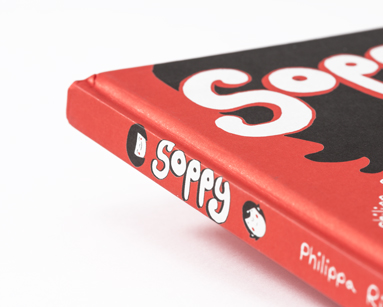
No Finish
On rare occasion you may opt to skip the cover finish. This provides a raw look and feel, but it’s important to note that it provides no protection, leaving your cover more susceptible to damage.
Binding
Binding is one of the most important steps of the whole process, as it has a big impact on both the style and quality of the finished product. Here we give a brief overview of the main types of binding, but please see the dedicated ‘Binding Methods‘ page for more detail.
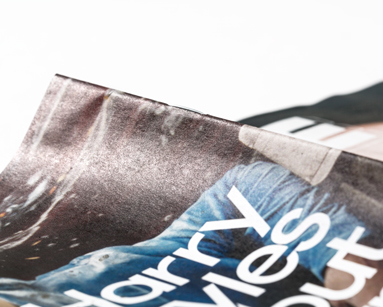
Saddle Stitched
You might have opted for saddle stitching as you’re creating a magazine or booklet which are suited to this method for their low cost and slick appearance. At this point your printed sheets will be folded in half and stapled in the centre, using one or two staples.
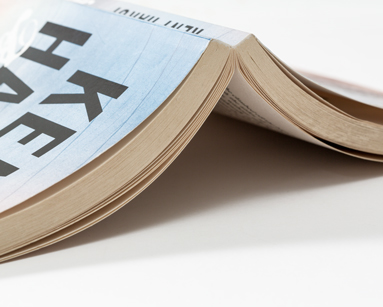
Perfect (Softcover) Binding
You could be printing a catalogue or a novel; perfect binding is suited to lots of different publications. At this stage your signatures will be trimmed, grouped together and be wrapped by the cover which is usually thin card. Your book will be flexible and can hold a high page count.
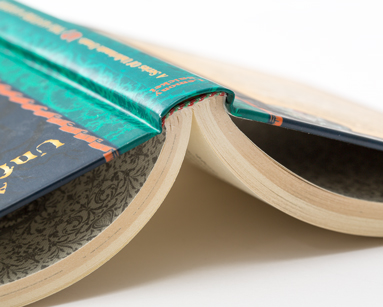
Casebound (Hardcover)
If you’re printing a really special publication you’ve likely chosen a casebound book. At this point your signatures will be grouped together and the case will be assembled from three pieces of board (for the front, back and spine). Both sections will then be joined together with end papers resulting in a durable and elegant book.
Quality Assurance & Drying
Most printing facilities will have a Quality Assurance department responsible for inspecting all printed parent sheets during the press run, monitoring the final product for defects, and flagging any issues early on in order to deter waste.
The quality control team follows the standards set by the printing facility, who ultimately decides the quality the product is required to meet. These quality assurance experts will sign off on color, bindery, and press runs by testing your product at random, during different steps of the process.
The final step in the offset printing process is to dry out your bound books. As you see below, all printed books are compactly stacked on top of each other using that pressure to halt pages from warping. This step is especially crucial for hard cover books; due to the moisture added in gluing and lamination, these covers are prone to curving if there’s no pressure to keep them flat while they dry.
Many printers will have a designated drying room with controlled temperature and humidity settings to ensure consistency in drying.